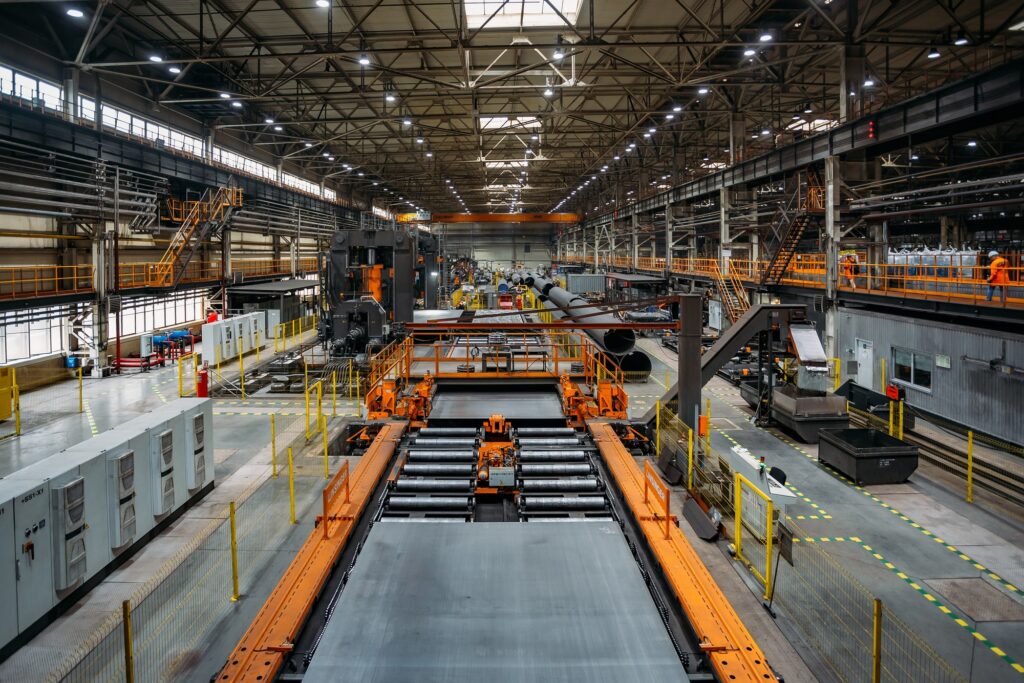
Unplanned downtime, when machines or equipment unexpectedly break down, is a big problem for factories and manufacturing companies. It’s way more than just a small issue – it’s like a giant money pit that can seriously hurt a company’s profits and stop it from growing. While everyone knows it means less stuff gets made, there are a lot of hidden costs that can really hurt a business.
The Obvious Costs
The biggest and most obvious cost of unplanned downtime is that less stuff gets made, so the company makes less money. When machines stop working, fewer products get made and sold. This often leads to the company having to pay workers overtime to catch up, which costs even more.
When a company can’t get orders out on time because of unplanned downtime, it can make customers unhappy. Late deliveries can hurt relationships with customers, damage the company’s reputation, and even cause contracts to be canceled or fines to be given out. In today’s world, where everyone wants things fast and on time, not being able to meet deadlines can be a huge problem.
Below the Surface
Beyond the obvious costs, there are other expenses that are harder to see. When machines break down, it often means having to pay extra for quick repairs or to rush order new parts, which can be very expensive.
For companies that make products that need to be stored carefully, like food or temperature-sensitive things, unplanned downtime can lead to waste. If these products can’t be made on time, they might spoil and have to be thrown away, which is a waste of money. Additionally, when production slows, it can cause delays for other companies that rely on those products, leading to even more financial problems.
The Intangible Costs
The problems of unplanned downtime go beyond just money. A company’s reputation, built over many years, can be ruined by delays and problems. Customers might not trust the company to get things done anymore, causing them to look for other options. This loss of trust is hard to fix and can lead to the company losing business.
Inside the company, unplanned downtime can even make employees unhappy. The stress of unexpected problems and the pressure to work extra to catch up can create a bad work environment. This can make people less productive, cause them to miss work, and even make them want to quit their jobs.
In industries with lots of rules, problems during downtime can lead to fines and legal trouble. Safety rules might be broken, environmental laws might not be followed, and quality control could suffer. The resulting penalties can be huge, adding even more financial stress to an already difficult situation.
Don’t Let Downtime Derail Your Production Line
Unplanned downtime is a complex problem for factories and manufacturing companies. It costs way more than just the lost money from less production. There are a lot of hidden costs and non-financial problems that can seriously damage a company in the long run.
Understanding all of these costs is important for making smart decisions about how to prevent problems, improve operations, and invest in reliable equipment. By taking steps to prevent unplanned downtime, like regular maintenance, using data to predict problems, and having backup plans, businesses can protect their profits, keep their good reputation, and continue to be successful in a world with a lot of competition.
Let ACS Help with All Your Production Equipment Repair and Maintenance Needs
Knowing what to do when you encounter unexpected downtime can be challenging, but you don’t have to do it alone. At ACS Industrial Services, we specialize in ensuring your equipment gets back up and running quickly.
With over 20 years of experience, ACS is a leading industrial repair service provider. We repair many different components of machinery across various makes and models. We provide a rapid turnaround time. Most repairs are back in your hands within 7-15 days, with our Rush Repair Service typically shipping in just 3-5 days.
When you choose us, you can expect real people, honest work, and accurate results. We showcase the dirty, gritty work aka magic that gets electronics back up and running. Contact us for a FREE evaluation and a no-obligation quote, or call (800) 605-6419.