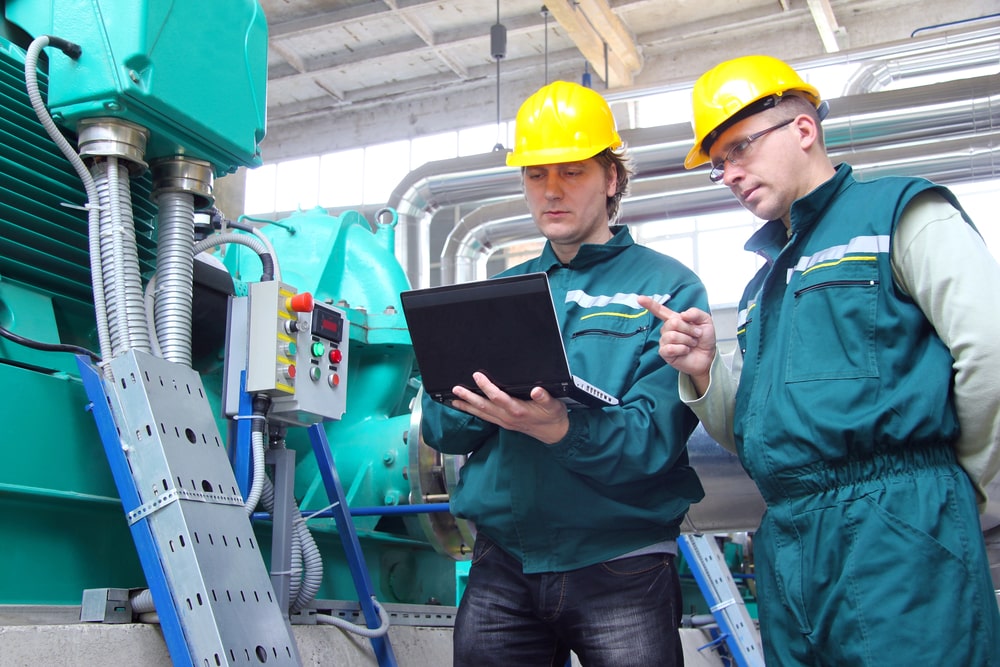
Production roadblocks are an unfortunate reality for businesses of all sizes and across all industries. These unforeseen obstacles can significantly disrupt operations, leading to delays, increased costs, and missed deadlines. A recent survey by Plant Services has identified the most common production roadblock: unexpected equipment failures.
Let’s take a closer look at the causes of these failures and determine how to prevent them, along with solutions for other common production roadblocks.
The High Cost of Unexpected Equipment Failures
Unplanned downtime due to equipment failures can be incredibly costly. It can result in lost production time, wasted materials, and increased labor costs. In some cases, it can even lead to safety hazards and environmental damage. These costs can quickly add up, potentially reaching hundreds of thousands of dollars per hour for large-scale operations. For small to medium-sized businesses, even a brief period of downtime can severely impact profitability and competitiveness.
Understanding the Causes of Unexpected Equipment Failures
There are several reasons why equipment might unexpectedly fail. A lack of preventative maintenance is a common culprit. When machines aren’t regularly inspected and serviced, small problems can escalate into major breakdowns. Aging equipment is another factor. As machines get older, their components can wear out and become more prone to failure.
Operator error is also a significant cause of equipment failures. This can include improper use of the machine, failure to follow safety protocols, or lack of training. Environmental factors, such as extreme temperatures or high humidity, can also contribute to equipment breakdowns.
Strategies for Preventing Unexpected Equipment Failures
The good news is that there are several strategies businesses can implement to prevent unexpected equipment failures. One of the most important is to establish a robust preventative maintenance program. This involves regular inspections, cleaning, lubrication, and replacement of worn parts.
Investing in modern, reliable equipment can also help to reduce the risk of failures. Newer machines often have advanced features, such as sensors and diagnostic tools, that can detect potential problems before they cause a breakdown. Thoroughly training operators on how to properly use and maintain equipment is another crucial step. This can help to prevent errors that might lead to failures.
Finally, it’s important to monitor and control environmental factors that might affect equipment performance. This might involve using climate control systems to maintain optimal temperatures and humidity levels.
Other Common Production Roadblocks and Solutions
While unexpected equipment failures are the most common production roadblock, there are other obstacles that businesses may encounter.
Supply chain disruptions can delay the delivery of essential materials and components, while labor shortages can make it difficult to find qualified workers.
Quality control issues can lead to defective products, which can be costly to repair or replace.
To address these challenges, businesses can diversify their supply chains, invest in workforce development, and implement rigorous quality control measures.
Final Thoughts
Production roadblocks are an inevitable part of doing business, but they don’t have to derail your operations. By understanding the common causes of these obstacles and implementing proactive strategies, you can minimize their impact and keep your production running smoothly.
Remember, the key is to take a holistic approach, addressing not only equipment failures but also other potential roadblocks such as supply chain disruptions, labor shortages, and quality control issues.
Let ACS Help with All Your Production Equipment Repair and Maintenance Needs
Knowing what to do when you encounter a production roadblock can be challenging, but you don’t have to do it alone. At ACS Industrial Services, we specialize in ensuring your production equipment remains in operation.
With over 20 years of experience, ACS is a leading industrial repair service provider. We repair many different components of machinery across various makes and models. We provide a rapid turnaround time. Most repairs are back in your hands within 7-15 days, with our Rush Repair Service typically shipping in just 3-5 days.
When you choose us, you can expect real people, honest work, and accurate results. We showcase the dirty, gritty work + magic that gets electronics back up and running. Contact us for a FREE evaluation and a no-obligation quote, or call (800) 605-6419.